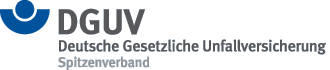
completed 06/2013
Frozen meat cutting machines are used to cut frozen blocks of meat into smaller parts in order for the material then to be processed further in mixers or mixer-mincers. The meat is cut into smaller pieces by blades arranged on a rotating drum. Since the cutting process entails high forces, the entire machine structure is subject to strong vibration, which is radiated in the form of noise. This results in relatively high noise exposure levels at the affected workplaces in meat-processing plants. In order for the noise emissions from the machine to be reduced, the dominant sources of noise were to be identified and suitable design measures developed for noise abatement. The results were to be suitable for transfer to other frozen-meat cutting machines. The objective was that of attaining a substantial reduction in the sound level in the areas in which these machines are used.
For recording of the initial situation, the noise emissions from a frozen meat cutting machine were measured under defined conditions at the manufacturer's premises. Since the noise situation under load could be achieved only for short durations, simultaneous sound pressure recordings were required at as many microphone positions as possible. Owing to the relatively short duration of operation under load, an acoustic camera was used to visualize the radiated sound, thereby enabling the primary sources of noise to be localized. In other words, the sound-level distribution was recorded by a microphone grid in the machine's remote field, and interpreted by determining of the transit time. Measurements were also performed of the structure-borne sound and the sound intensity, in order to determine the proportions of the discrete sources of noise within the total radiated sound. The results enabled a number of suitable noise-abatement measures to be identified. These were incorporated into the design of a new frozen meat cutting machine. The effectiveness of the noise abatement measures was tested by means of sound emission measurements.
A relatively large noise pulse occurs as soon as the frozen blocks are ejected on the feed table. Further noise sources identified were the drive motor fitted to the base plate of the enclosure, and the knife shaft connected to it by toothed belts. In order for the shock pulse that occurs when material is fed in to be reduced, damping of the table plate or increasing of its rigidity by means of reinforcing ribs was recommended. For attenuation of the excitation of the machine enclosure by the drive motor and the knife shaft, it was proposed that a special connecting frame be engineered between the motor and the knife shaft, or that the knife shaft be driven directly. Further proposals for noise abatement were lining of the meat pan with damping material and facing of the machine enclosure with soundproofing material. In a preliminary test, the machine enclosure was faced with soundproofing material and a number of surfaces lined with damping material. However, these measures resulted only in minor noise abatement, owing to problems with coupling of the damping linings. A frozen meat cutting machine was therefore designed from the ground up with consideration for the lowest possible sound emission. This design included direct drive of the knife shaft, a larger, solid cutting drum, and a composite feed table. However, since the new design was implemented in much larger machines, each of which is able to process two frozen meat blocks in a shorter time, the measured noise emission values cannot be compared directly to those of the standard machine. A noise level at idle around ten db(A) lower than that of the smaller, standard machine studied was measured on the new machine design. Allowing for the cutting capacity of the machine, the noise emission under load is around four db(A) lower.
-cross sectoral-
Type of hazard:noise/vibrations
Catchwords:noise
Description, key words:noise abatement, noise measurement technology, meat-processing industry, localization of noise sources, noise emissions, frozen meat cutting machine