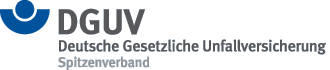
completed 06/2012
Hazards are prevented by the maintenance of an adequate safety distance between an operator and hazardous zones on machinery. Electro-sensitive protective equipment (ESPE) detects the position of a person, thus ensuring that when the safety distance is violated, the hazard is eliminated in time before the person reaches the hazardous zone. Safety distances were defined many years ago in the EN ISO 13855 Type B standard, "Safety of machinery - Positioning of safeguards with respect to the approach speeds of parts of the human body", and are dependent upon the form of approach, size and nature of the safeguard. The normative provisions were set out for ESPE with a two-dimensional safety zones, e.g. light curtains, light barriers, laser scanners and 2D vision systems. In recent years however, vision systems with a three-dimensional safety zone have become available for safety applications. These systems offer greater flexibility in the configuration of safety zones. They differ from ESPE with a two-dimensional safety zone not only in their geometry, but also in that they are mounted for example on the ceiling and monitor the latter from above, rather than being present within the work area. As a result, the worker is less conscious of the active safety zones. The project is intended to use virtual reality (VR) methods in order to examine whether the safety distances intended for 2D safety zones are also suitable for application to ESPE with 3D safety zones. The ultimate aim is to develop a concept for the safety distances of ESPE with 3D safety zones.
A survey was first conducted which established that beyond the normative provisions, little other studies of practical relevance to the subject had been performed. As a result there were no further issues identified. ESPE with a 3D safety zone was simulated within the project. Ideal values for the relevant parameters, such as spatial resolution and response time, were postulated in order for the movements of the head and both hands to be tracked and the limited space in the VR laboratory to be exploited to the full. The idealized ESPE model reflects the anticipated state of the art in five years' time. The VR laboratory at the Institute for Occupational Safety and Health of the German Social Accident Insurance (IFA) uses a tracking system sourced from Vicon which identifies the position of the observer's head by active illumination of markers affixed to the 3D glasses. The addition of further markers enabled this existing tracking system to be used for rapid and precise measurement of the positions and velocities of the head and the two hands. The 3D ESPE could thus be simulated virtually with a number of different 3D safety zones and no longer had to be physically installed and configured, a time-consuming process. Calculation of the safety distances to EN ISO 13855 is based on several factors. These should be reassessed in the context of the 3D ESPE. The focus of the project lay upon measurement of the motion speed of the person as influenced by the lower presence of the safety equipment in the working area and the possible absence of a visible safety zone. For this purpose, an assembly workplace was simulated in mixed reality at which twenty test subjects each fitted up an actual assembly frame in twenty work cycles according to a defined pattern and placed it on an actual rotary table. The performance of tasks by a virtual robot was then simulated in temporally distributed collaboration. Each test subject repeated this study with a cuboid safety zone typical of 2D ESPE and a spherical safety zone which exploits the benefits of 3D ESPE. The safety zone was marked either by an outer warning field or by adhesive tape on the floor or was not marked at all. Besides motion data, violations of the safety zone, and performance parameters (speed and correctness of the assembly task and of the cognitive pattern recognition task), the perception of presence and the mental strain were recorded and analysed by means of questionnaires.
The test subjects violate the cuboid substantially more frequently than the spherical safety zone. No differences in motion speed were noted between the geometries. The different forms of marking of the 3D safety zones revealed differences in the number of safety zone violations. Owing to the wide differences between the test subjects, no conclusions can be drawn at this stage regarding whether visible floor markings or an invisible warning field are more effective. The test subjects generally move fastest when the safety zone is marked on the floor. A visible floor marking may therefore increase the subjective feeling of safety. The measured average maximum motion speeds per working cycle are slightly below the currently applicable value of 1,600 mm/s in EN ISO 13855. Concrete recommendations for adjustment of the normative provisions for safety distances for 3D safety equipment cannot therefore be made at this stage based upon the results of the present project. More detailed studies are required in order to clarify whether the greater number of injuries in the cuboid safety zone are the result of the poorer perceptibility (cognitive causes) or simply of the less favourable geometry (ergonomic causes). What for example is the effect of 3D visualization of the safety zones by semi-transparent presentation in the VR scene? Review of the results on a simulated actual workplace could provide further information and support transfer to the field. The perception of presence by the test subjects, which serves as an indicator of the quality of VR simulation, is strong, even somewhat exceeding the values found in the international literature. Completion of the assembly task and immersion in mixed reality caused no impairing symptoms of simulation sickness such as headaches, nausea or dizziness.
-cross sectoral-
Type of hazard:mechanical hazards
Catchwords:machine safety, man-machine interface, technical protective measures (exposure reduction/ protective devices)
Description, key words:virtual reality, safety distances, electro-sensitive protective equipment (ESPE), non-contact, protective devices, machines, hazardous zones, detection zone, safety zone, vision system, work zone, virtual reality (VR), tracking, approach, position, velocity, resolution, usability, ergonomics